What Products Are Made from Medical Injection Molding?
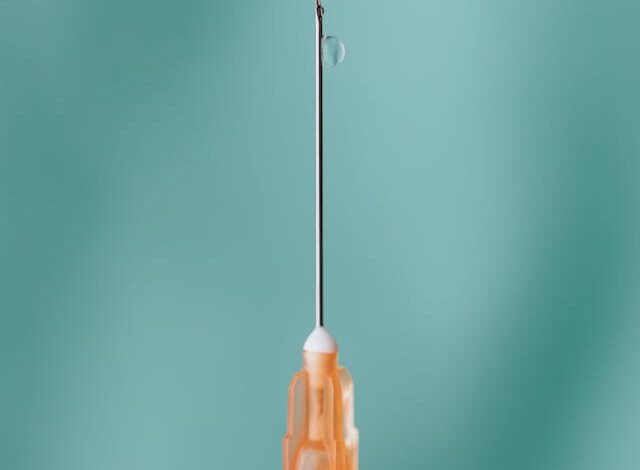
In today’s rapidly advancing medical field, the manufacturing process plays a crucial role in ensuring the availability of high-quality medical products. Among the various manufacturing techniques utilized in healthcare, medical injection Molding stands out for its efficiency, precision, and versatility. This article explores the products fabricated through medical injection Molding and sheds light on their significance in modern healthcare.
Introduction to Medical Injection Molding
Medical Injection Molding is a manufacturing process employed to produce intricate and precise components used in medical devices and equipment. It involves injecting molten material into a mould cavity, where it solidifies to form the desired product shape. This method allows for the mass production of medical products with consistent quality and dimensional accuracy.
Importance of Medical Injection Molding in Healthcare
The significance of medical injection Molding in healthcare cannot be overstated. It enables the production of a wide range of medical products essential for diagnosis, treatment, and patient care. From disposable items to complex surgical instruments, medical injection Molding plays a pivotal role in meeting the demands of the healthcare industry.
Common Products Made from Medical Injection Molding
Syringes and Needles
Among the most recognizable products manufactured through medical injection Molding are syringes and needles. These essential tools are used for administering medications, drawing blood, and delivering vaccines. Medical injection Molding ensures the production of sterile, precise, and cost-effective syringes and needles, vital for medical procedures worldwide.
Medical Devices and Instruments
Medical injection Molding is instrumental in producing various medical devices and instruments used in hospitals, clinics, and laboratories. This includes components for respiratory devices, surgical instruments, diagnostic equipment, and more. The versatility of injection Molding allows for the fabrication of complex geometries and intricate designs required for these devices.
IV Components
Intravenous (IV) therapy is a cornerstone of modern medical care, and many components used in IV administration are manufactured through medical injection Molding. This includes IV catheters, connectors, infusion sets, and drip chambers. The precise molding capabilities ensure the integrity and functionality of these critical components, contributing to patient safety and comfort.
Drug Delivery Systems
Drug delivery systems, such as inhalers, insulin pens, and infusion pumps, rely on components produced through medical injection Molding. These systems facilitate the controlled administration of medications, ensuring accurate dosing and patient compliance. Injection Molding allows for the production of intricate drug delivery mechanisms with tight tolerances and consistent performance.
Advantages of Using Medical Injection Molding
Medical injection Molding offers several advantages over traditional manufacturing methods, making it the preferred choice for medical product fabrication. These advantages include:
- Precision: Injection Molding allows for the production of highly precise and intricate components with tight tolerances.
- Efficiency: The high-speed production capabilities of injection Molding ensure rapid turnaround times and cost-effective manufacturing.
- Versatility: Injection Molding can accommodate a wide range of materials, including thermoplastics, elastomers, and bioresorbable polymers.
- Consistency: The automated nature of injection Molding results in consistent product quality and dimensional accuracy, essential for medical applications.
- Scalability: Injection Molding is easily scalable, allowing for the production of large volumes of medical products to meet market demands.
Materials Used in Medical Injection Molding
A variety of materials are used in medical injection Molding, each selected based on its specific properties and requirements. Common materials include:
- Polycarbonate: Known for its strength, transparency, and heat resistance, polycarbonate is commonly used in medical device housings and components.
- Polypropylene: With excellent chemical resistance and flexibility, polypropylene is ideal for syringes, IV components, and medical packaging.
- Polyethylene: This versatile material is used in medical tubing, containers, and implantable devices due to its biocompatibility and durability.
- ABS (Acrylonitrile Butadiene Styrene): ABS is frequently used in medical instrument handles and housings, offering a balance of strength and impact resistance.
Quality Control in Medical Injection Molding
Ensuring the quality and safety of medical products fabricated through injection Molding is paramount. Stringent quality control measures are implemented throughout the manufacturing process, including material testing, mould validation, process monitoring, and product inspection. Compliance with regulatory standards such as ISO 13485 and FDA regulations is essential to guaranteeing product efficacy and patient safety.
Future Trends in Medical Injection Molding
The field of medical injection Molding continues to evolve with advancements in materials, technologies, and processes. Future trends include the adoption of bioresorbable polymers for implantable devices, the integration of additive manufacturing techniques for personalized medical products, and the implementation of automation and robotics for enhanced efficiency and precision.
Sustainability Practices in Medical Injection Molding
As environmental concerns grow, sustainability practices in medical injection Molding are gaining traction. Manufacturers are exploring biodegradable and recyclable materials, optimizing energy usage, and implementing waste reduction strategies to minimize the environmental impact of the manufacturing process.
Conclusion
In conclusion, Medical Injection Molding plays a vital role in the production of various essential products used in healthcare settings. From syringes and medical devices to IV components and drug delivery systems, the versatility and precision of injection Molding contribute to the advancement of modern medicine. As technology continues to progress, the future of medical injection Molding holds promise for further innovation and improvement in healthcare delivery.